An Inventory Management Form is essential for efficient stock control and tracking. It helps businesses monitor inventory levels, streamline stock movements, and minimize errors. This guide explores the key elements of creating, customizing, and using forms to ensure optimal inventory operations. Whether it’s an Inventory Transfer Form for relocating stock between locations or a general inventory sheet, this guide provides detailed examples to enhance accuracy and efficiency. Learn practical tips for organizing your inventory records and aligning them with your operational goals. Simplify your processes while maintaining precise control over your inventory flow.
Download Inventory Management Form Bundle
What is an Inventory Management Form?
An Inventory Management Form is a structured document used to track and manage stock levels, movements, and availability. It ensures accurate record-keeping for items in storage or transit. Businesses use these forms to streamline inventory transfers, monitor usage patterns, and forecast needs. These forms improve organization, reduce errors, and enhance decision-making. By maintaining clear and concise records, they help businesses meet operational demands effectively while optimizing resources.
Inventory Management Format
Date:
[Submission Date]
Inventory Manager:
[Manager’s Name or Department]
Inventory Details:
- Item Name: [Name of the Product]
- SKU/ID: [Unique Identifier]
- Current Stock Level: [Number of Units]
- Reorder Level: [Minimum Units Required]
- Supplier Details: [Supplier Name and Contact Information]
Movements:
- Date of Entry: [Restock Date]
- Quantity Received: [Number of Units]
- Issued To: [Department or Individual]
- Remaining Stock: [Current Inventory]
Remarks:
[Notes regarding damages, delays, or quality issues.]
Authorized By:
[Manager’s Signature and Date]
Small Business Inventory Management Form
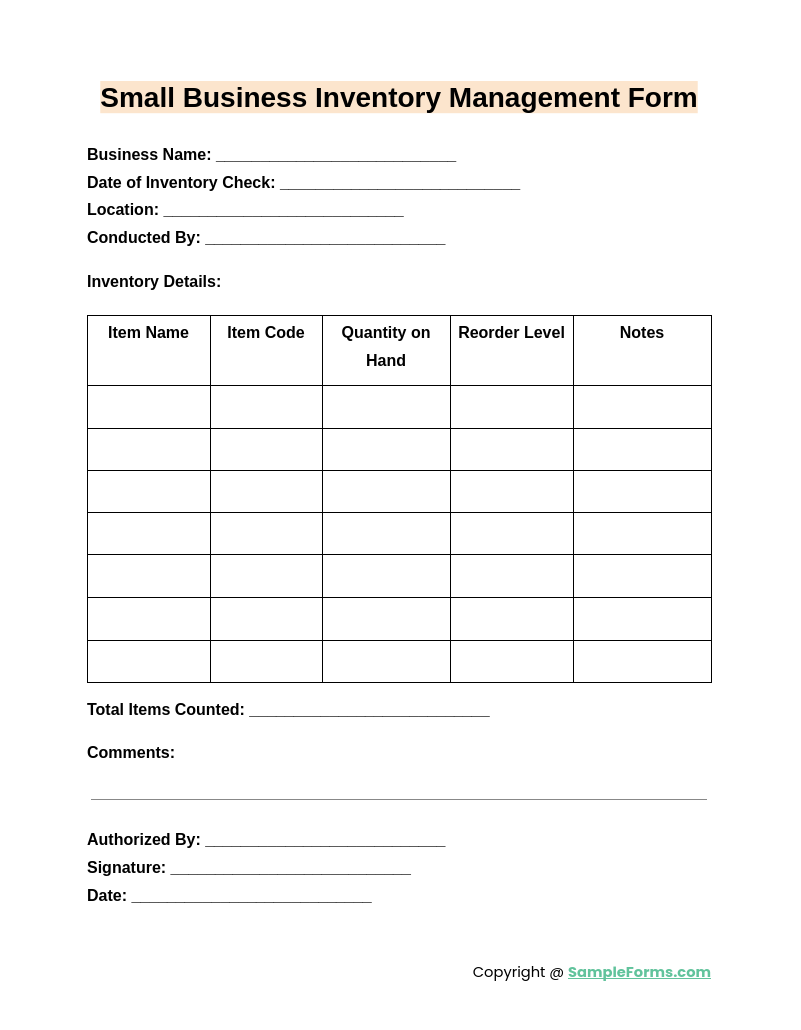
A Small Business Inventory Management Form helps track stock effectively, ensuring smooth operations. It integrates elements like a Management Appraisal Form to evaluate and enhance inventory strategies for streamlined processes and minimal errors.
Construction Site Inventory Management Form
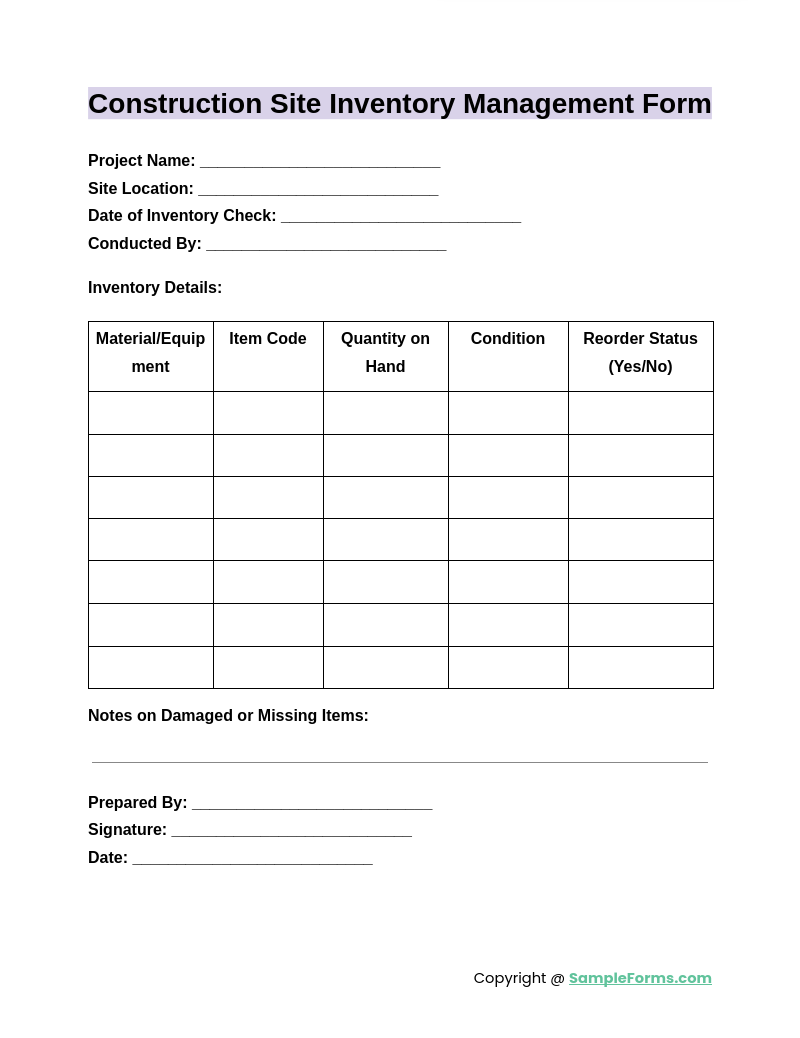
A Construction Site Inventory Management Form organizes materials and tools for on-site projects. Similar to a Construction Management Form, it tracks usage, availability, and reordering needs, ensuring seamless project execution and efficient resource utilization.
Equipment Inventory Management Form
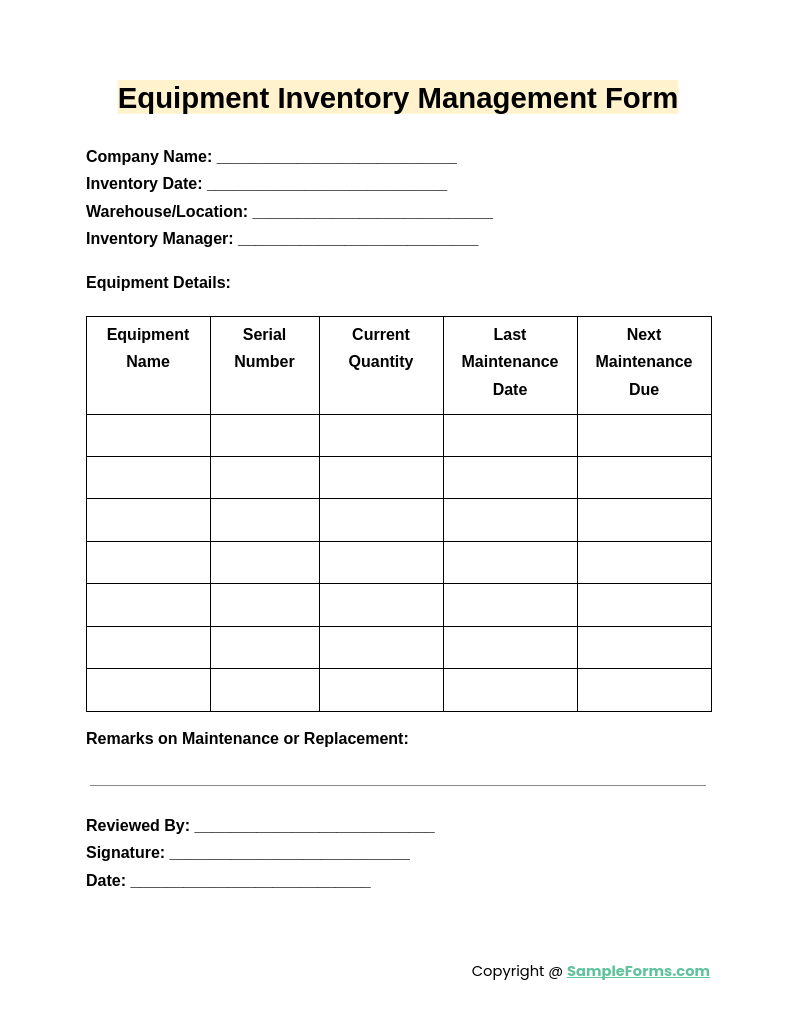
An Equipment Inventory Management Form monitors equipment location, condition, and usage. It incorporates details like a Kitchen Management Form for industries such as hospitality or catering, ensuring tools are properly tracked and maintained.
Inventory Stock Management Form
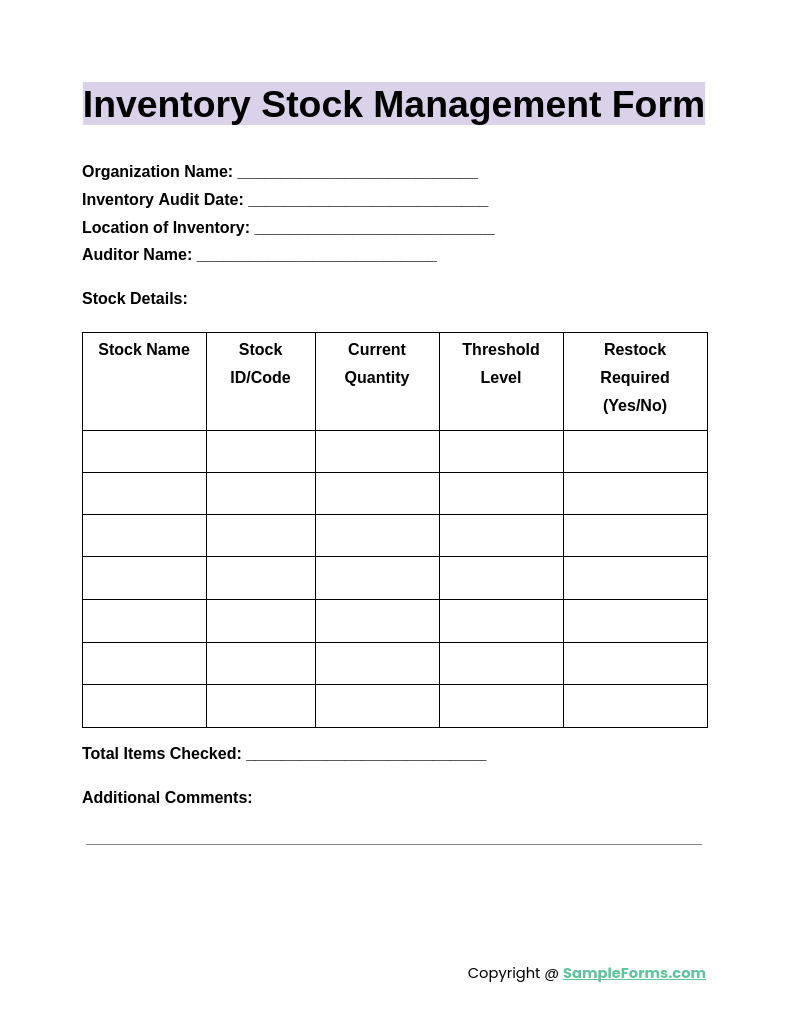
An Inventory Stock Management Form records stock levels, movements, and reorder points. Designed for all sectors, including a Business Management Form setup, it optimizes inventory control and prevents overstocking or shortages
Browse More Inventory Management Forms
1. Sample Inventory Management Form
2. Management of Inventory Sample Form
3. Sample Management of Inventory Form
4. Inventory Management Sample Form
5. Generic Management of Inventory Form
6. Generic Inventory Management Form
7. Material Inventory Management Form
What are the components of inventory management?
Effective inventory management ensures smooth operations and cost efficiency. The core components include planning, tracking, storing, and analyzing inventory processes. Key points include:
- Inventory Planning: Determine demand, reorder levels, and stock requirements to avoid shortages or excesses.
- Inventory Tracking: Monitor inventory movements using barcodes, RFID, or software for real-time accuracy, similar to a Management Agreement system.
- Storage Management: Optimize storage space, ensuring safety and accessibility of goods.
- Supply Chain Coordination: Align suppliers and logistics to meet inventory needs efficiently.
- Performance Analysis: Regularly review data to identify inefficiencies and improve inventory strategies.
How to create a form for inventory?
An inventory form standardizes data collection, ensuring accuracy in tracking stock levels. Steps to create an effective form include:
- Identify Required Data: Include essential fields like item name, quantity, and location for clear tracking, akin to a Management Agreement Form.
- Choose a Format: Decide between paper or digital forms based on your business needs and scalability.
- Include Sections: Organize the form with categories for easy navigation and understanding.
- Add Automation Features: Use software for automated calculations, such as total stock value or reorder notifications.
- Test the Form: Ensure the form is user-friendly and captures all necessary data accurately.
What are the Major inventory management techniques?
Three primary techniques optimize inventory control, ensuring businesses meet demands without overstocking. These techniques include:
- Just-in-Time (JIT): Order inventory only when needed to minimize holding costs, similar to an Event Management Form system for on-demand requirements.
- ABC Analysis: Categorize inventory into three groups (A, B, C) based on value and importance.
- Economic Order Quantity (EOQ): Calculate the optimal order quantity to minimize total costs.
- FIFO and LIFO: Use First-In-First-Out (FIFO) or Last-In-First-Out (LIFO) methods based on inventory type.
- Dropshipping: Transfer customer orders directly to suppliers to avoid holding inventory.
What are the types of inventory management?
The four inventory management types ensure businesses address specific needs, including storage, tracking, and demand fulfillment. Key types include:
- Raw Materials Inventory: Tracks components used in production.
- Work-in-Progress Inventory: Monitors unfinished goods during production processes.
- Finished Goods Inventory: Manages ready-to-sell items, similar to a Restaurant Management Form for menu items.
- Maintenance, Repair, and Operations (MRO): Oversees supplies used to maintain production.
- Perpetual Inventory System: Uses real-time tracking for continuous updates.
What are the main steps in inventory management?
Effective inventory management involves planning, execution, monitoring, and analysis to ensure operational success. The four main steps include:
- Inventory Planning: Forecast demand and plan reorder points to avoid stockouts or overstocking.
- Stock Organization: Arrange inventory systematically for easy access and tracking, utilizing methods like a Management Report Form.
- Tracking Movements: Use technology for accurate inventory tracking during receiving, storage, and shipping.
- Reconciliation: Regularly compare physical inventory with recorded data to identify discrepancies.
- Performance Review: Analyze inventory reports to optimize processes and improve overall efficiency.
What does an inventory list look like?
An inventory list typically includes item names, quantities, locations, and descriptions. For example, a Management Risk Assessment Form might include safety equipment details for tracking.
How to keep track of inventory?
Track inventory by categorizing items, using technology like barcodes, and updating a Stock Requisition Form regularly for accuracy and efficiency.
Is there an app to keep track of inventory?
Yes, inventory management apps like Sortly help track stock levels. You can also use features similar to a Stock Transfer Form for real-time updates.
What is the rule of inventory?
The key rule is maintaining balance: avoid overstocking or understocking, akin to structured processes in a Stockroom Requisition Form for precise control.
How to do an inventory checklist?
Create an inventory checklist by listing items, recording quantities, and noting conditions. A Supply Contract Form ensures formal agreements for inventory-related terms.
How to calculate inventory?
Calculate inventory by tracking opening stock, adding purchases, and deducting sold items, similar to the data captured in a Supply Request Form.
What is ABC inventory analysis?
ABC inventory analysis classifies items by value: ‘A’ (high value), ‘B’ (moderate value), ‘C’ (low value), optimizing resources like a Supply Requisition Form.
How to manage stock inventory?
Manage stock by forecasting demand, tracking movements, and organizing storage systematically. Use a Restaurant Business Plan Form for better inventory alignment.
What is the correct order for inventory management setup?
The setup order includes planning, categorizing, tracking, and analyzing stock levels, as outlined in an Action Plan Form for seamless operations.
How to manage stock inventory?
Efficient stock management includes monitoring stock flow, using technology, and maintaining accurate records. Processes like an Event Planner Form improve operational clarity.
An Inventory Management Form simplifies stock control and record-keeping, making it indispensable for businesses. Whether used for daily tracking ensures efficiency and accuracy. From managing inventory transfers to forecasting needs, these forms enhance workflows and reduce errors. By adopting well-designed forms, businesses can meet operational goals, streamline processes, and maintain better stock visibility. Investing time in crafting effective inventory forms significantly boosts productivity and reduces costs.
Related Posts
-
FREE 25+ Insurance Forms in PDF | MS Word
-
Migration Form
-
FREE 50+ Facility Forms in PDF | MS Word
-
FREE 36+ Partnership Forms in PDF | MS Word (doc.)
-
FREE 51+ Assignment Forms in PDF | MS Word | XLS
-
FREE 50+ Letter Forms in PDF | MS Word
-
FREE 32+ Holiday Forms in PDF | MS Word
-
Withdrawal Form
-
Visitors Form
-
Delivery Form
-
FREE 30+ Nonprofit Forms in PDF | MS Word
-
FREE 31+ Therapy Forms in PDF | MS Word | XLS
-
FREE 52+ Bid Forms in PDF | MS Word | XLS
-
Shipping Form
-
Vendor Form